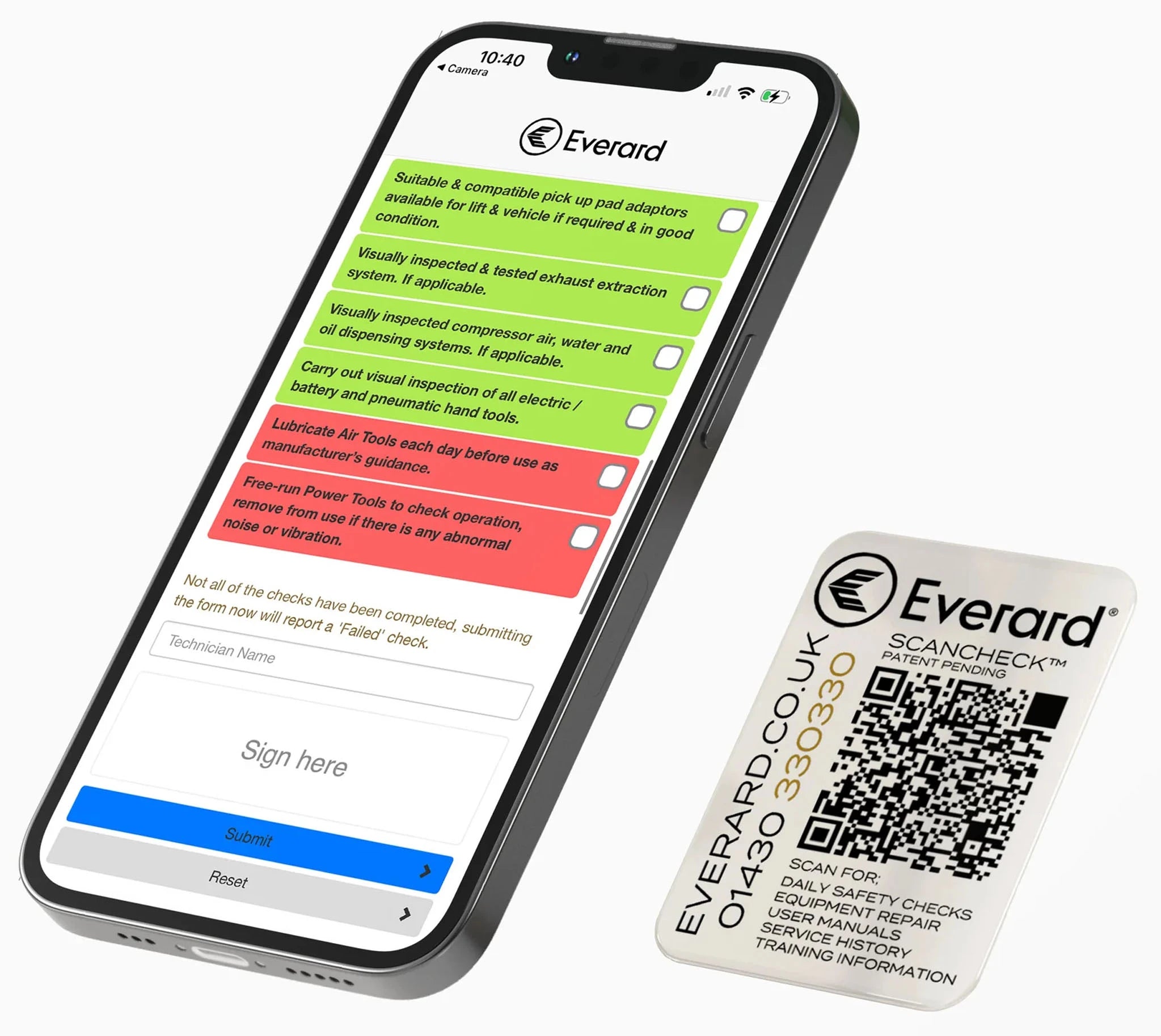
What is SCANCHECK?
SCANCHECK™ is an easy-to-use system designed to simplify equipment management in workshops. From daily safety checks to service history and repair requests, it brings everything together in one place for technicians and managers alike.
Daily Safety Checks
Technicians can complete daily safety checks using a simple checklist system. Add a name, signature, and submit. All checks are compiled into a single report, ensuring nothing is missed.
Request Repairs
Quickly report faults by requesting repairs through the app. Add a fault description, contact details, and even photos or videos to ensure engineers are fully prepared.
User Manuals & Service History
Access a digital library of user manuals and service history for each piece of equipment. View past inspections, calibration certificates, and detailed job sheets.
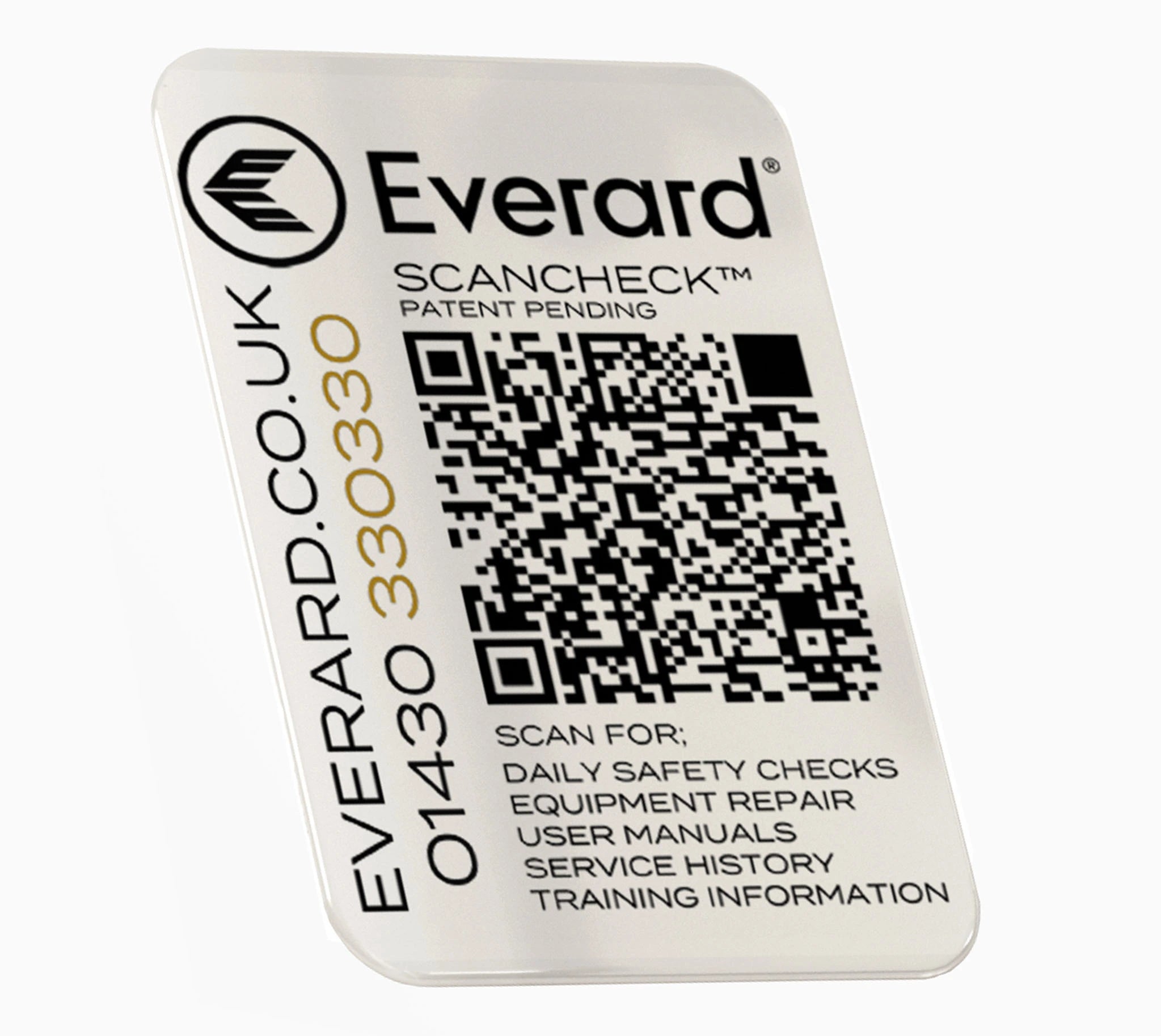
It All Starts with the QR Code
The SCANCHECK system revolves around a unique QR code, which is placed on every piece of equipment Everard maintains in the workshop. A quick scan with any mobile device, users can access everything they need - whether it's performing safety checks, requesting repairs, viewing service history, daily lift checks or service manuals.
The QR code connects the equipment to the SCANCHECK platform, ensuring accurate tracking, easy access to information, and seamless management, all in one place.
The SCANCHECK Dashboard
A Complete Overview at Your Fingertips
The SCANCHECK dashboard provides workshop managers with a detailed view of equipment status and activity. It allows you to track inspections, review service history, monitor daily checks, and ensure everything is operating smoothly.
Weekly visibility of job/repair progress, allowing you to plan work around engineer visits.
Quick-reference status of daily checks—passed, failed, not checked, etc.
Quick access to PDF reports for each lift, each day, including the technician’s name, signature, and time stamps.
Immediate visibility of ongoing job/repair work, providing information such as awaiting part, visit scheduled, etc.
Review all outstanding quotes. From here, you can consolidate quotes into single or multiple visits (depending on urgency or parts needed), or decline recommended quotes—providing clarity on any outstanding quotes per site.